BACnet, EnOcean and DALI communication for higher implementation flexibility and easier operation
Issue 01-2016:
read all articles online
read as pdf
The German appliance manufacturer Miele is building a new office complex in four construction stages at the company headquarters in Gütersloh. The importance of choosing the right building automation solution for fast and flexible implementation of the project as well as optimized operation is shown in the first completed building. This new facility was automated using PC control from Beckhoff and supported by BACnet, EnOcean and DALI communication.
The first of the four new administration buildings has a total of four office floors, each with an area of 1,000 m2. Concrete core activation for the basic heating/ cooling load, floating ceiling panels and a ventilation system for implementing the change of air have been implemented. In addition to the classic automation of the heating, ventilation and air conditioning systems, the entire room automation is integrated into the automation system, including sun protection with exterior louvered blinds and and lighting. The technical building infrastructure was planned by the Bielefeld-based engineering firm Schröder & Partner and implemented by system integrator Brüggemann from Versmold.
Automation stations control HVAC and room functions
Located in the basement of the building is a central air conditioning plant for the supply of fresh air to all four office floors. The Cold water requirement for the air conditioning system, the concrete core activation and the floating ceiling panels is met by the factory’s own cold water supply network. The heating energy is similarly provided by a local heating supply.
An automation station is responsible for controlling and regulating the complete HVAC plant in the basement. In order to optimize the efficiency of the energy generation and distribution, the control of all generation and distribution systems is optimized to suit needs through communication with the automation stations for room automation on the floors of the building. For a proactive control of the concrete core activation, the forecasts from the online service wetter.com were integrated in addition to the current weather information.
On each office floor there is an automation station in the form of a CX2020 Embedded
PC, to which the room climate, lighting and sun protection systems are connected. The utilization times of the office floors are specified by timer schedules. Outside of the regular utilization times the building is switched to an economy mode; i.e. the ventilation and air conditioning system is switched off and the room temperatures are reduced to a low energy level. within the utilization times the room temperature setpoint values are raised to the Comfort energy level.
Simple wireless networking of control elements and sensors
The users of the open space work areas can lower or raise the room temperature of individual zones within a small range using EnOcean room control units. The air volume in the floors is controlled by means of flow rate regulators, depending on the air quality. All the windows on a floor are provided with EnOcean-based window contacts. If the windows are open the entire open space area is switched to the “Protection” operating mode. When Protection mode is active the room temperature setpoint values are lowered to 6 °C for the heating operation and raised to 35 °C for the cooling operation. By means of the flow rate regulators the air volume is reduced to a minimum in Protection mode.
The communication range of EnOcean wireless signals is at least 30 m, which can considerably reduce the cabling in a building. This has had a positive impact in many respects according to Jürgen Meierarnd: “In order to successfully accomplish Miele’s new open-space concept (instead of conventional office and workplace structures), the concrete floor plan of the individual floors had to be finalized at a very late stage. For reasons of time, therefore, a wire-connected installation of light switches, sensors, etc. would have been very difficult. The EnOcean wireless technology offered us maximum flexibility here. Further advantages are the reduction in costs due to the reduced cabling and the correspondingly lower fire loads.
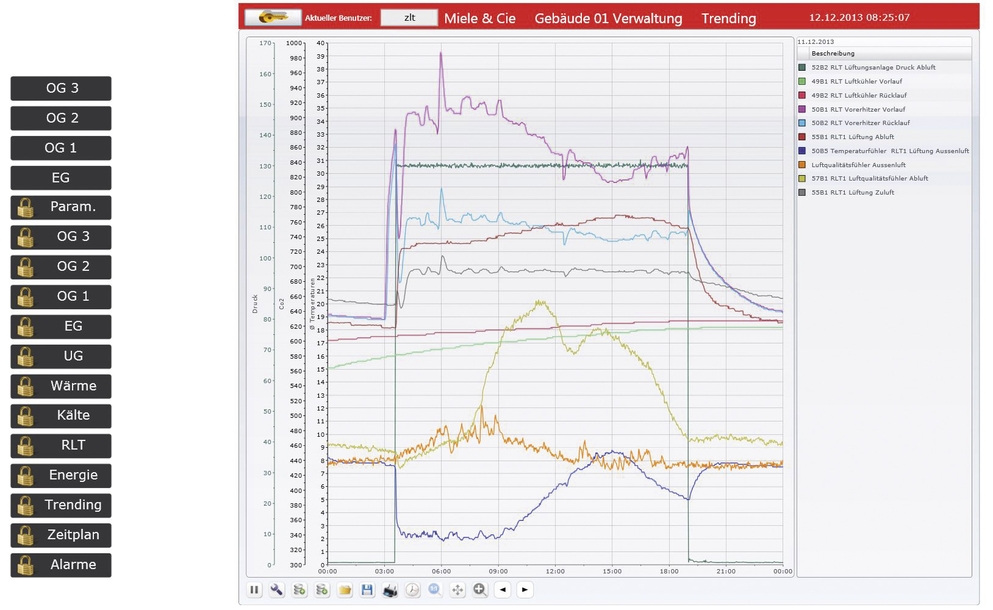
Detailed trend display of the RLT system data (image source Brüggemann)
Energy-efficient building operation
In case of bright sunlight outside of the regular utilization times, the blinds are lowered by the automatic thermal control. This reduces the cooling load of the building and saves energy for the generation of cooling water. If the room temperature drops below the setpoint value of the Comfort level, the automatic thermal control automatically raises the blinds in order to use the energy input from the sun to heat the rooms.
In order to create optimum working conditions for the PC workstations in the offices, the “Sun protection” program is activated when the room is in use. The sun protection lowers the blinds to a defined position. The louver angle is aligned in relation to the position of the sun so that glare is prevented whilst still allowing the maximum amount of natural daylight to enter. This saves energy for artificial illumination. The automatic functions of the sun protection system can be manually overridden by the building users by means of EnOcean buttons. Following the manual actuation of an EnOcean button, the blind controller switches back to automatic mode on the expiry of a time parameterized by the operator.
The automation station on the fourth floor is connected by a serial communication terminal to a weather station via the Modbus-RTU protocol. The weather data is transmitted via BACnet/IP to the other BACnet stations. By means of the weather information for wind force, precipitation and outside temperature, the blinds are protected against storm and ice damage and are automatically raised in case of danger.
The open space areas are lit by standard lamps at the workplace. The lighting is switched on by an occupancy sensor integrated in the lamps. The standard lamps are also capable of EnOcean communication and are integrated into the building automation system. In order to minimize the energy consumption for lighting the corridors, the lighting systems there are integrated into the automation system by means of a KL6811 DALI interface from Beckhoff. EnOcean brightness sensors measure the light intensity. The presence of people in the corridors is likewise detected by an EnOcean sensor. The lights are thus switched on only when required.
Easy control and flexible design of a complex system
In addition to the EnOcean room control units, the rooms can also be controlled on the floor level by a touch panel (15-inch CP2916 Control Panel). The automation stations on the floors consolidate the data from the DALI, EnOcean and Modbus-RTU devices. There are a total of 15,000 BACnet objects within the five BACnet servers for the room and plant automation. A new BACnet management and control level (MCL) for the entire Miele works in Gütersloh is currently under construction. In the programming of the BACnet servers, however, care was taken in advance to ensure that the future connection of further office buildings to the new MCL at Miele will go without a hitch.
All relevant data and parameters are made available with TwinCAT BACnet/IP via BACnet objects. Also, energy meters are integrated via the KL6781 M-bus terminal from Beckhoff for energy optimization. To implement the project, the room automation functions were programmed in accordance with the new VDI 3813 directive. winCAT libraries and program templates from Beckhoff, including the required BACnet objects, facilitate the engineering even of complex systems and room automation functions.
New articles in Smart Building
Top articles
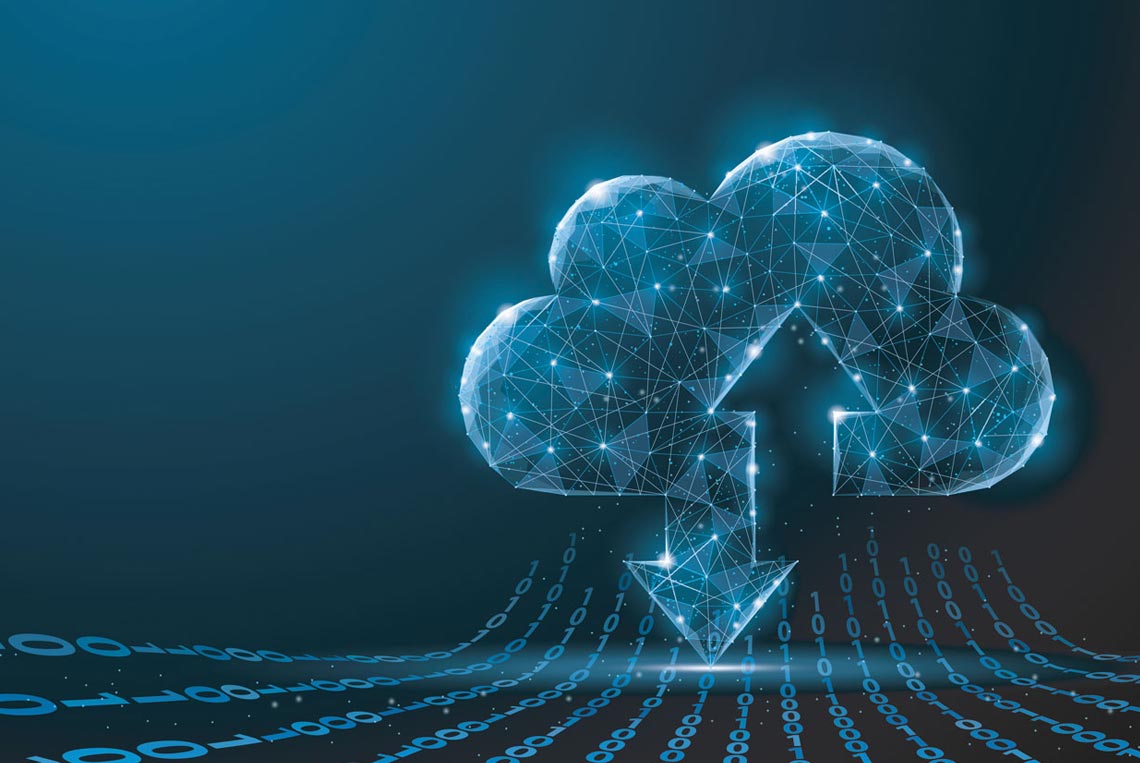