EnOcean sensors for factory operation monitoring and visualization
Issue 01-2022:
read all articles online
read as pdf
EnOcean sensors are used in many different scenarios.The following project at the Kyoto plant of an Osaka-based company in Japan serves as an example. The manager of the Kyoto factory planned to visualize the operational status of production equipment and the progress of processed parts in the factory in order to improve the company’s DX and efficiency in the manufacturing process.
The following goals were set:
- Visualization of equipment’s degree of capacity utilization
- Reduction of robot and equipment downtime
- Visualization of workers’ on-site presence/absence
The project team was tasked with visualizing the production facilities and the efficiency of manufacturing processes. This meant introducing and linking the SCADA system supplied by MXTechnologies with Inaba Electric Industry’s Signal Watcher and Optex’s Presence Detection Sensor (CPD), which are commercially available as EnOcean sensors.
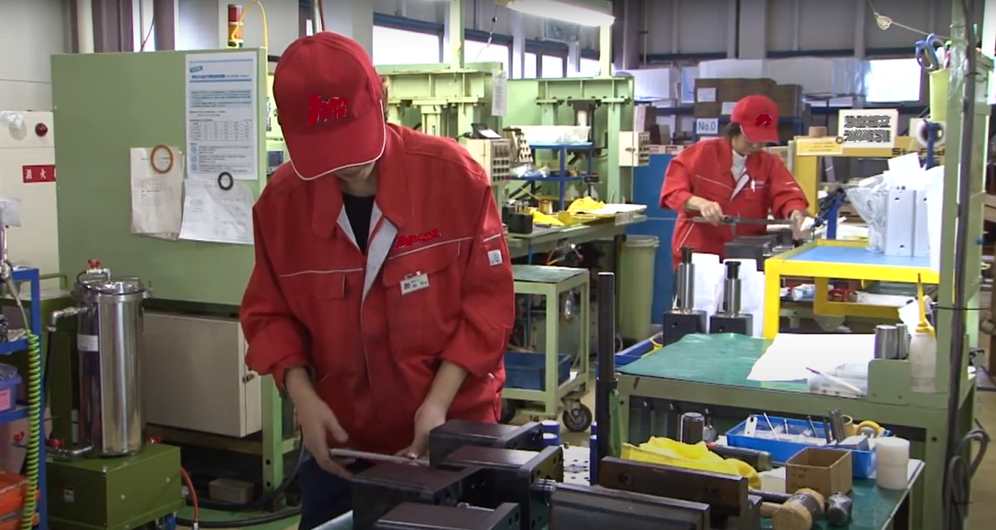
Initial approach to implementation
The company’s business is manufacturing and selling hydraulic cylinders for various general industrial applications and supplying cylinders to machinery and equipment manufacturers in Japan and overseas. The company is unique in its production methods, and some of its products can be shipped only four days after an order is received.
Current operational status and effectiveness
When producing cylinders, there are tens of thousands of possible combinations of finished products and several common parts. Consequently, a thoroughly standardized and systematized production system must function properly in order to meet JIS standards.
That’s why the company has already semi-automated the production process using its own host computer system and has introduced a retrofit IoT visualization system (SCADA system, etc.). This system displays the status of equipment and workers on production lines throughout the plant with a view to consistently increasing the equipment utilization rate and production volume.
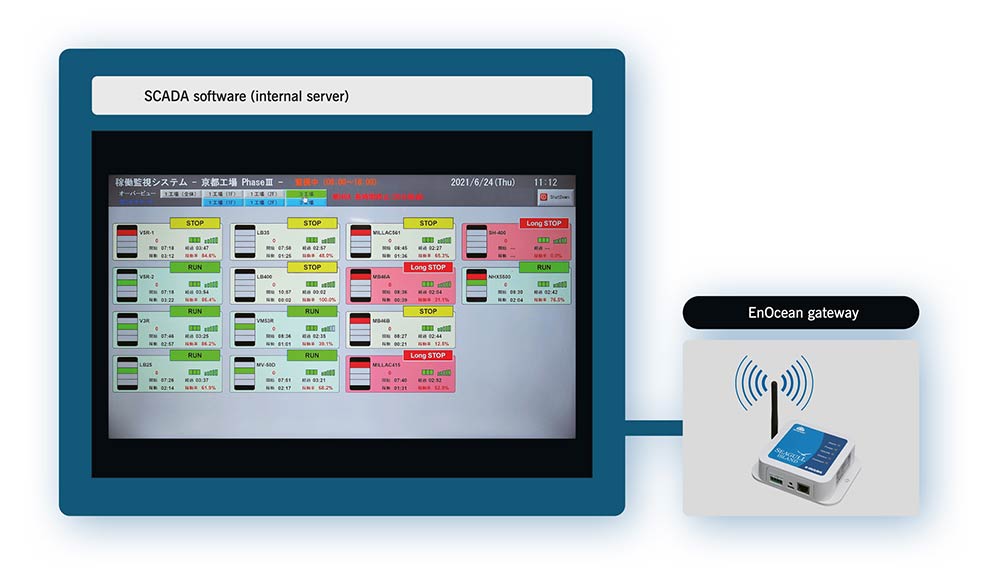
The Kyoto factory has a number of machine tools, processing robots, and machining centers that have been in operation for about 40 years, all of which are now equipped with the Signal Watcher. Even in the case of modern equipment that can be directly linked to data, operational information is obtained from indicator lights because direct data linkage requires additional spending just to receive the information. Additionally, the information received from the equipment needs to be integrated into the company’s system, which increases the time and effort required to start operation.
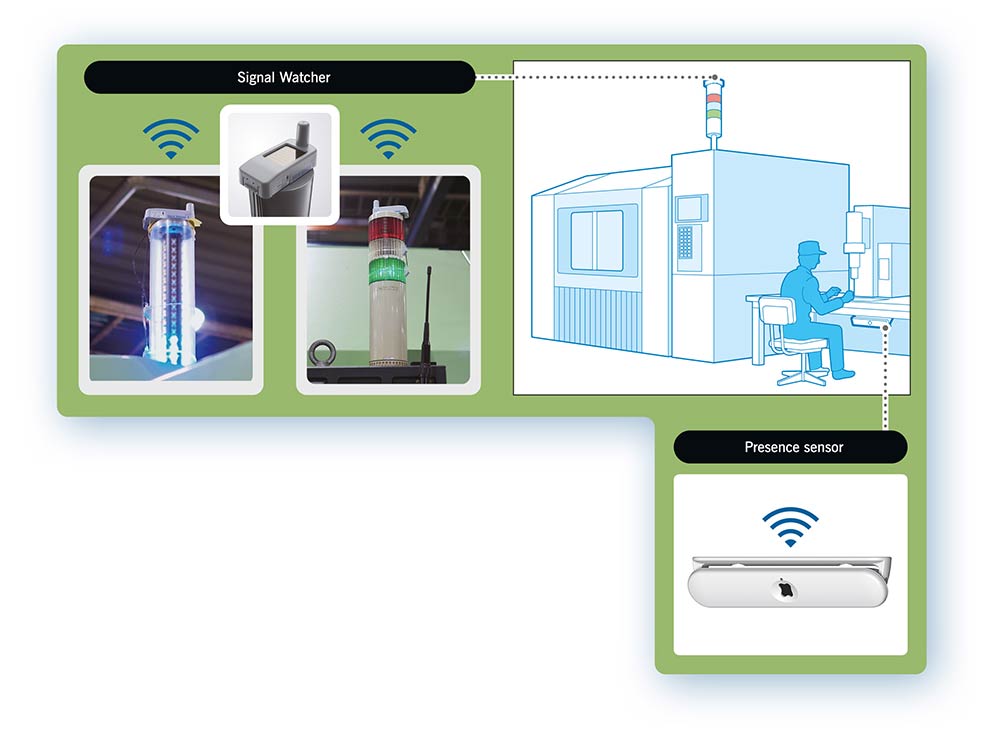
Presence detection sensors are also installed on the front of some workstations to track the relationship between workers’ presence and the facility’s utilization rate as well as time left unattended (rush time) in case of any errors. For this purpose, a system was adopted that utilizes EnOcean wireless sensors, which consume very little power thanks to energy harvesting technology. This approach eliminates the need for post-installation maintenance, requires no modifications, and allows on-site managers to easily check the operational status of equipment and workers in the factory.
Future developments
The operation monitoring system currently in place at the Kyoto plant has been well received internally, and the company is planning to expand the system to its Osaka plant as well. The company also plans to test the use of the wireless acceleration sensor “Multisensor,” to predict equipment failure and to detect the deterioration and failure of metal processing equipment at an early stage. In addition to this customer, Inaba Electric Industry is planning a new lineup of sensors and EnOcean products in order to meet the challenges of the factory automation industry with EnOcean technology.
h
New articles in Industry
Top articles
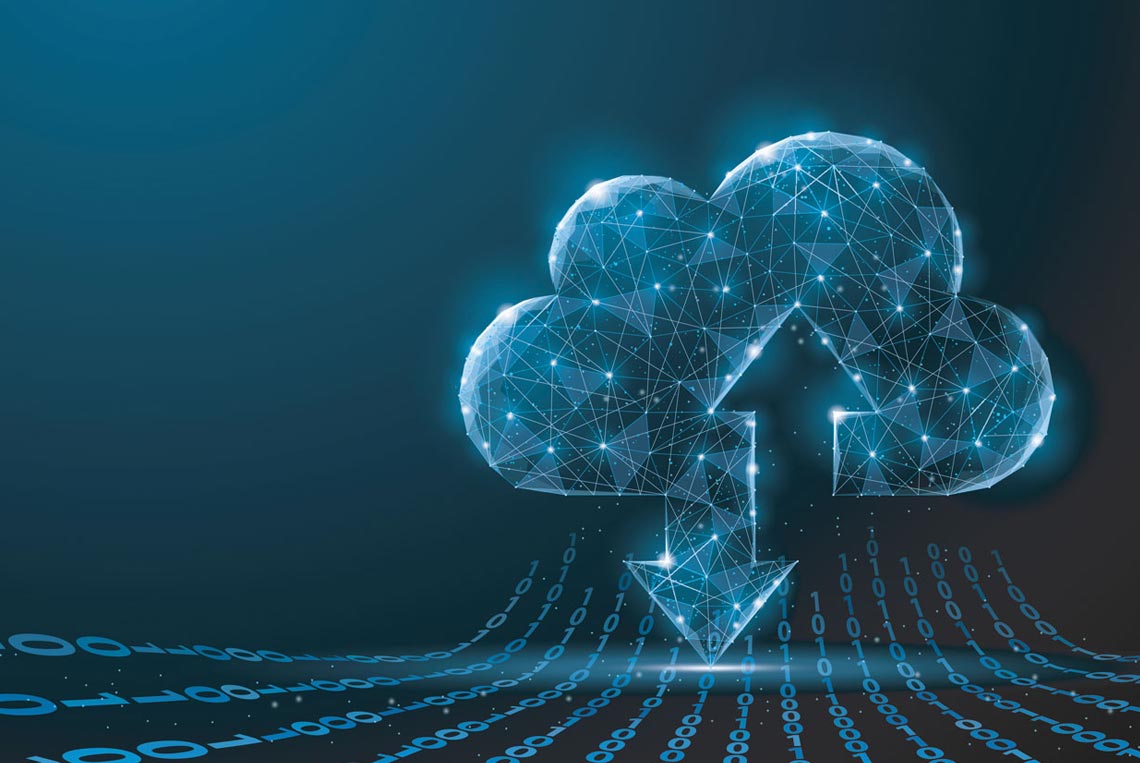