Cutting a considerable amount of CO2
Issue 02-2015:
read all articles online
read as pdf
The Daiwa House multi-tenant distribution center (DLP Sagamihara), which was established in December 2013, is gathering attention as an environmental friendly distribution center, cutting a considerable amount of CO2 compared to conventional facilities.
The five floor building encompasses an area of 100,000 m2 and integrates the Daiwa Logistics Energy Management System (D-LEMS), which not only measures the energy consumption for electricity and water supply but also supervises and controls lighting, air-conditioning and ventilation, securing an energy-efficient operation.
Originally, there was no integrated management system interconnecting the whole facility, making an efficient operation very difficult. Therefore, Daiwa House Industry and Uchida Yoko jointly developed the D-LEMS system, based on Uchida Yoko’s Network Building Intelligent System, NBIS. Using this system, a building control network, such as LONWORKS, can be seamlessly connected to a TCP/IP network and devices from different manufacturers with different specifications can be connected and controlled in the same network topology all at once.
Managing the facility via tablet
In DLP Sagamihara the facility managers and the tenants get a tablet PC, by which they can monitor and manage all facilities inside their rented area. Inside the building’s warehouse even the shortest distance from one end to the other is 70.5 meters, in certain cases the distance is as long as 249.6 meters. This means that it takes quite an effort for the tenants to walk to the switches installed on the walls. Therefore, all facilities, including lighting or ventilation, can be controlled from anywhere inside the building using a tablet PC connected to the wireless LAN. In addition, there are plans to reduce the building’s energy consumption by always switching off lights when not needed, for example.
Integrated management
For ventilation, an air backflow system is set in place, where the air is drawn into an underground pit and cycles from there to the upper floors. This system is connected to the D-LEMS and can therefore also be controlled remotely. The upper floors’ temperature is thereby lowered by approximately one to three degrees Celsius in the hot summer months, so that air conditioning becomes more effective and energy-efficient. However, the installation of an additional air-conditioning is optional. The system’s flexible design allows the tenant to integrate and control air-conditioning by D-LEMS, even if it is added later on.
Temperature and humidity measurement
In the logistics sector, the traceability of the warehouse environment is highly important, for example regular temperature and humidity are measured to prevent dew formation due to increased humidity. In the past, temperature and humidity were usually measured by wired and analog solutions, which restricted a later expansion or the movement of sensors.
In addition, the points of measurement differ from tenant to tenant depending on the type of product stored in the warehouse and the tenant’s overall business conditions. The EnOcean-based sensors were the best solution. They require no wires or batteries and can therefore be flexibly placed without the need for regular battery changes. The number of installed sensors can be adjusted anytime, so that the building management is adapted to the tenants’ needs.
Experience an integrated management platform
D-LEMS, which was installed in the DLP Sagamihara, is an integrated monitoring and building control system. In order to control the facility properly, all information, including temperature and humidity values, needs to be measured appropriately and the controlled computers or switches have to be handled flexibly. The EnOcean devices and connected NBIS use open technology and can therefore be implemented easily. Further information on this system and practical examples can be experienced in the Uchida Yoko showroom.
New articles in Smart Building
Top articles
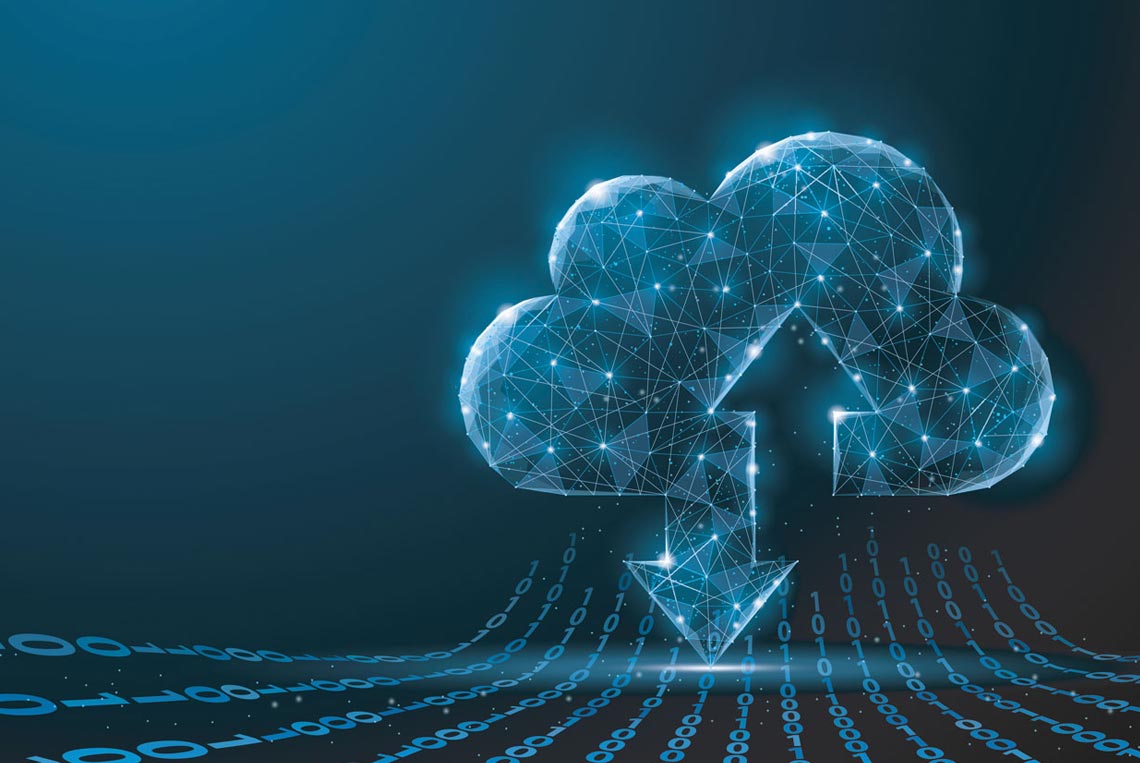