Production Hall of Fame – DALI and WAGO light management systems
Issue 02-2016:
read all articles online
read as pdf
Workplace lighting systems must meet strict requirements. They have to be reliable and efficient and also create an optimum atmosphere as needed. Powerful automation technology offers additional benefits by eliminating programming work during commissioning and assisting technicians when it comes to repurposing and maintaining the systems. WAGO recently implemented a solution of this type in its new punching shop in Minden, Germany.
It measures 25,000 square meters, making it approximately the same size as three soccer fields. WAGO invested approximately 20 million euros in its new punching shop. The building, where furniture was built until the end of 2014, has been completely gutted over the past few months. The production hall also received a new lighting system during the course of the renovations.
Automation is the basis for light control
The WAGO light management system is based on the new generation of PFC200 controllers, to which I/O modules from the WAGO I/O SYSTEM 750 series were added. The key element in this interplay is the DALI bus terminal, which integrates up to 64 DALI luminaires and up to 16 DALI sensors into the system. Along with up to ten DALI bus terminals that can be operated on one controller, additional I/O modules can be connected in series for each task or each signal, for example to measure energy in three-phase power grids, for EnOcean energy-harvesting wireless pushbuttons or digital input/output signals.
Due to the total area of WAGO’s production hall in Minden, a total of four automation systems are used for lighting in the facility. The four controllers are installed in separate control cabinets on the equipment platform in the middle of the building. The controllers communicate with each other and with the control center via Modbus TCP.
Modern web visualization
WAGO has implemented a special, userfriendly application on each controller that eliminates the need for users to do any programming. All settings are made with a click of the mouse during commissioning as well as during operation. Because the graphical user interface is accessed with a standard browser, there is no need to install software locally on a PC.
During the first configuration step, DALI addresses are assigned to all DALI users: the luminaires, sensors, switches and pushbuttons. They are then linked to EnOcean wireless pushbuttons or digital input and output values. The luminaires can also be grouped in so-called virtual rooms – in the Minden production hall, for example, these are the traffic routes or areas with production machines.
A wide range of functions
The control software of the WAGO light management system provides a wide range of options during operation that contribute to energy efficiency, comfort and occupational safety. In addition to the standard functions of dimming and turning the lights on and off, ingenious features can be implemented in connection with corresponding sensors:
- A daylight controller, for example, dims the lights depending on the current ambient brightness, while presence detectors ensure that the lights are on only when someone is actually in the illumination zones.
- Not least, a scheduler lets users define detailed light scenarios for any day of the week and for any time of day, for example a central “lights off” scenario for the end of the work day.
Combined with DALI, the WAGO light management system offers benefits that go beyond actual light control – for maintenance, to give one example. Operating hour counters for each luminaire, for instance, permit predictive planning in predefined intervals. The luminaires also report defective lamps on request. The lamp installed in each luminaire is stored in the software, as well as an indication of which tool is needed to replace it.
Flexible light management
EnOcean technology is used, for example, in the flexible office zones and in the production areas in the WAGO facility in Minden. Among other things, the upgradable window contacts communicate with the control system in this manner.
The main reasons for using EnOcean technology are that the components are easy to upgrade and can also be easily repurposed later on. For example, pushbuttons for lights are mounted wherever the people actually go – for example, in the hallway leading to the break room and at the outer door. If these routes change over time, the EnOcean components are also flexible. This approach works so well because the systems are wireless and batteryless and permit a free logical assignment of functions.
New articles in Smart Building
Top articles
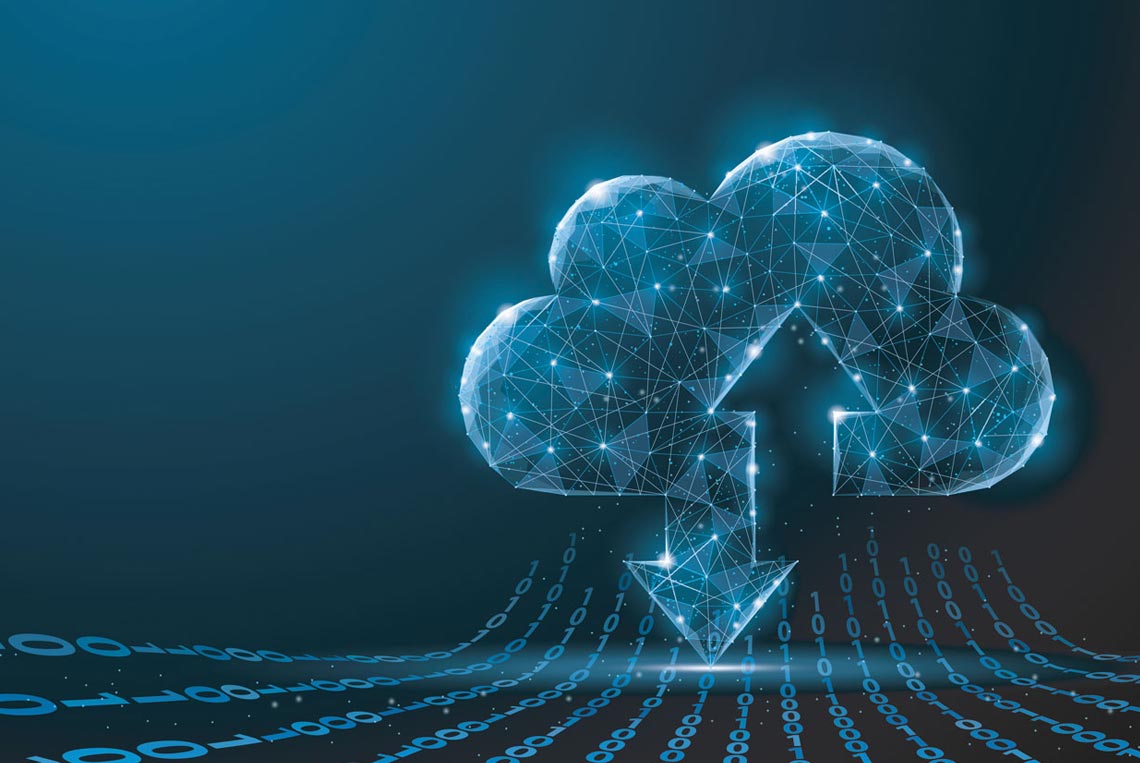