Predictive maintenance – early detection of imminent breakdowns
Issue :
read all articles online
read as pdf
In classic building automation installations, sensors have been reliably controlling shading systems and light controllers as well as heating, ventilation and air-conditioning systems (HVAC) for many years, based on the detected data. Linked with the Internet of Things (IoT), today’s sensors not only supply data but also form nothing less than the basis for digitalizing buildings and technical installations.
Whereas companies were initially concerned mainly with optimizing their processes with IoT projects, today they also focus on developing new business models. Facility management is a good example of this. In addition to pure building management activities, some facility management companies are already offering new digital services, thanks to the IoT. Wireless and maintenance-free sensors network the building and provide a digital, 360-degree view to make room utilization and cleaning transparent, for example, and to adapt these functions to actual demand. With its sensors, EnOcean supplies the raw data for the necessary analyses on cloud-based platforms. Along with this development, the demand-oriented predictive maintenance concept is capturing the attention of facility managers.
What is predictive maintenance?
Motors and machines of all types and sizes form the heart of buildings and industrial plants. Without them, everything would grind to a halt. The heating system and elevators would no longer run, the cooling system in a data center would fail, and production would temporarily come to a standstill.
That’s why facility managers and plant operators have long been experimenting with ways to optimize technical installations economically and with maximum effect – that is, with as few breakdowns as possible.
New technical developments, including those in the area of sensors, place the predictive maintenance concept at the top of the agenda. Although this approach is not really anything new, the current state of the art now makes it ready for widespread use with a positive cost/benefit ratio.
The so-called predictive maintenance approach detects the condition of machines based on sensors, links it with historic data or standard values and derives predictions for possible failure from this information. Predictive maintenance saves money by preventing (unnecessary) standstills and production losses ahead of time. As a result, regularly set service intervals (preventive maintenance) or worst cases—namely, ad-hoc repairs during a failure—can be avoided. Data-based, predictive maintenance also makes it possible to plan spare parts deliveries and the deployment of service technicians in keeping with demand.
Interoperable components
In predictive maintenance, many components must interact perfectly in order to calculate the best possible time for service. The basic requirement is to collect data with sensors. In real time, they supply the information needed to evaluate the current condition and identify future trends. This includes, for example, deviations from standard values and characteristics in relation to temperature, humidity or vibration.
Possible application scenarios:
- Temperature sensors on control cabinets in data centers raise the alarm when an overheating situation, and thus a breakdown, is imminent.
- Sensors measure the temperature at the cables of a fan to determine how long the motor will continue to run, based on the current characteristic.
- Moisture sensors in boiler rooms monitor water leaks.
- Temperature sensors monitor pumps, brakes, transmissions, motors and cooling units.
- Differential pressure sensors measure the condition of filters.
- Sensors measure the fill level of a container by “counting” the pump operations, detecting each current pulse that triggers a pump operation.
The raw data from the sensors is supplied via a gateway to the cloud, where it is visualized for further analysis. Using the digital twin of the building or industrial plant thus created, the technical facility management team determines which products demonstrate features of an imminent breakdown.
Saving money with self-powered wireless sensors
Surveys show that many companies cite lack of data as a stumbling block when it comes to IoT projects such as predictive maintenance. The fact is, this data is available within the companies and just has to be collected and made usable. Of course, this process must also remain within defined cost parameters.
Radio-based sensors are an excellent option for collecting data, particularly in existing buildings and industrial plants. They eliminate the need for expensive retrofits, a cost that is due primarily to running cables in ceilings and walls. The wireless sensors can also be flexibly mounted on built-in technical installations, even in locations that are not easily accessible.
In some cases, hundreds to thousands of sensors are needed, depending on the project size. This makes self-powered wireless sensors that use energy harvesting technology and obtain their energy directly from their surroundings a sensible choice. The EnOcean sensors, for example, use small solar cells, kinetic energy or temperature differences to transmit the data to the cloud wirelessly. There are no follow-up costs resulting from the need to regularly replace the batteries.
Finding the right partner
IoT projects are generally complex, although there is an increasing trend toward standardization. In some cases, ready-made IoT packages are already available from various collaborating manufacturers. When hardware and software manufacturers, system integrators and cloud service providers work together, the customer reaps significant benefits. The EnOcean Alliance acts as a nucleus for such endeavors. An ecosystem of more than 400 partners has formed within the Alliance that can successfully implement IoT projects such as predictive maintenance. Long-lasting partnerships and certified, open standards and interfaces ensure the interoperability of the different products and solutions and thus contribute to project success.
New articles in Smart Spaces
Top articles
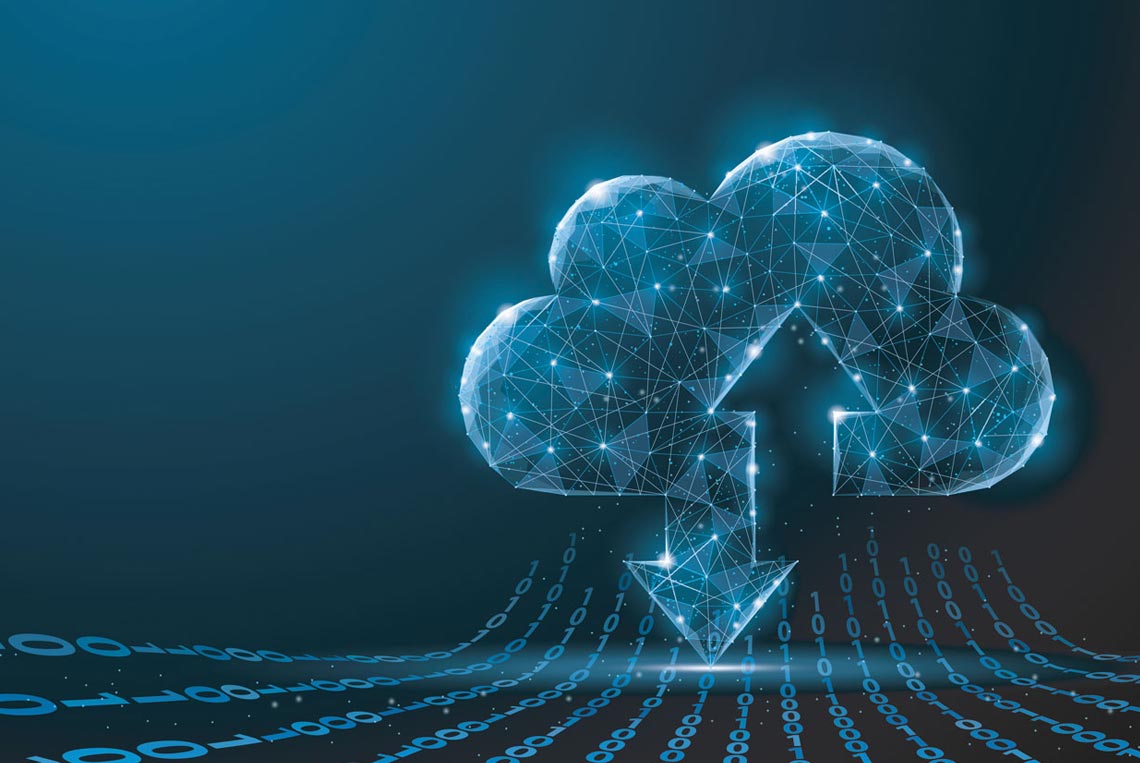